From waste plastic to naphtha
A process in 3 steps
Our pyrolysis process of waste plastic can be explained in three simple steps:
1. Solid waste plastic is heated up and transferred into a melt.
2. Under the absence of oxygen and more heat introduction it starts to crack, the resulting short hydrocarbon molecules are released as a hot pyrolysis gas.
3. Cooling down this pyrolysis gas results in pyrolysis oil. In our case, this pyrolysis oil meets the quality criteria of naphtha.
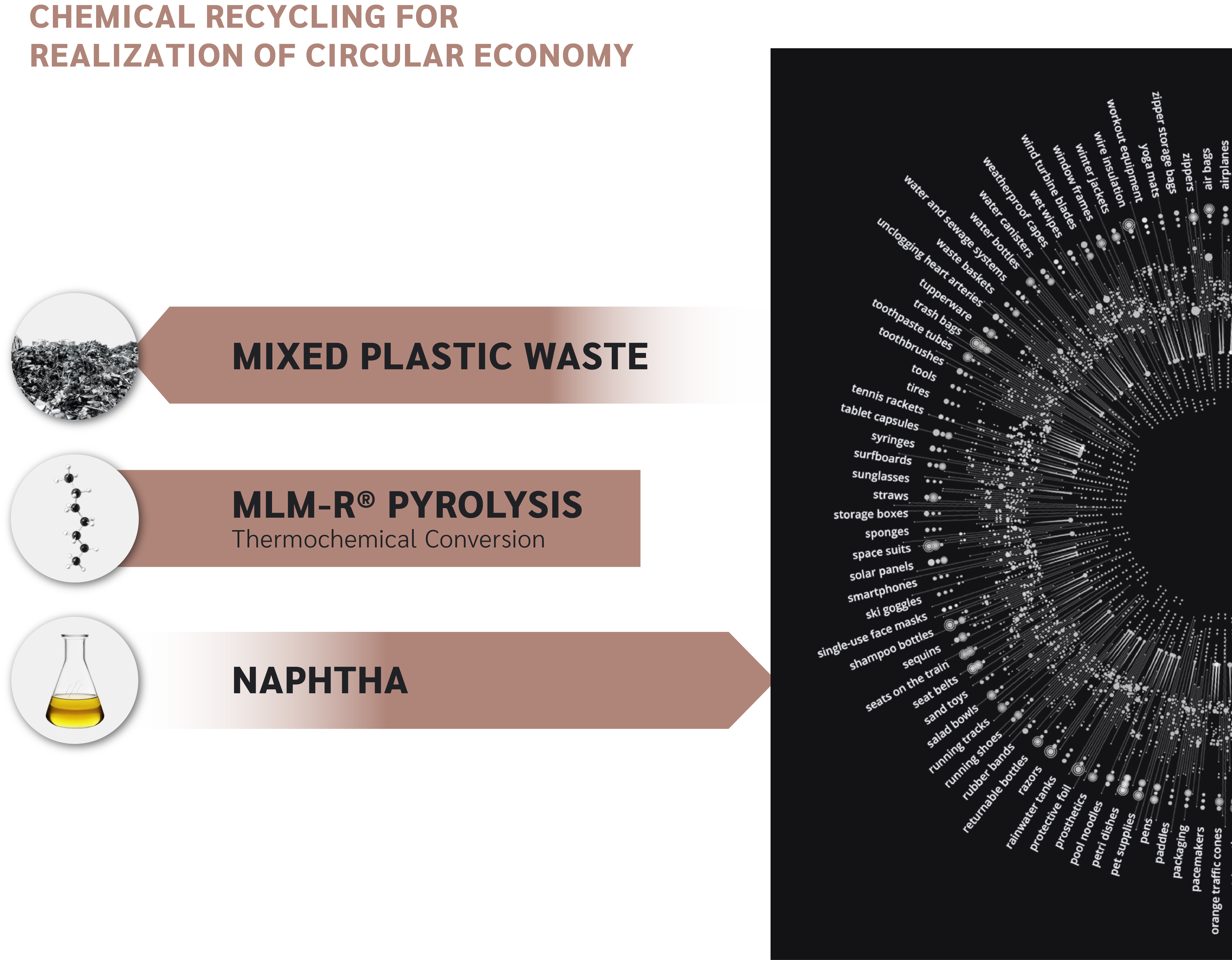
The MLM-R® Loop
Continuous pyrolysis process
1. Waste plastic is introduced into the reactor
2. Heat carrier is transferred to the regenerator
3. Heat carrier is reheated and reintroduced into the reactor
4. Pyrolysis gas is routed to the condensation module

Technical realization of the pyrolysis conditions
Our heating method of reaction volume
The low thermal conductivity of polymer is the fundamental challenge for the pyrolysis process. Mastering the heat transfer into the plastic mass is the key to creating optimal and homogeneous process conditions.
Our direct heating method overcomes this intrinsic challenge of the low thermal conductivity of polymers.
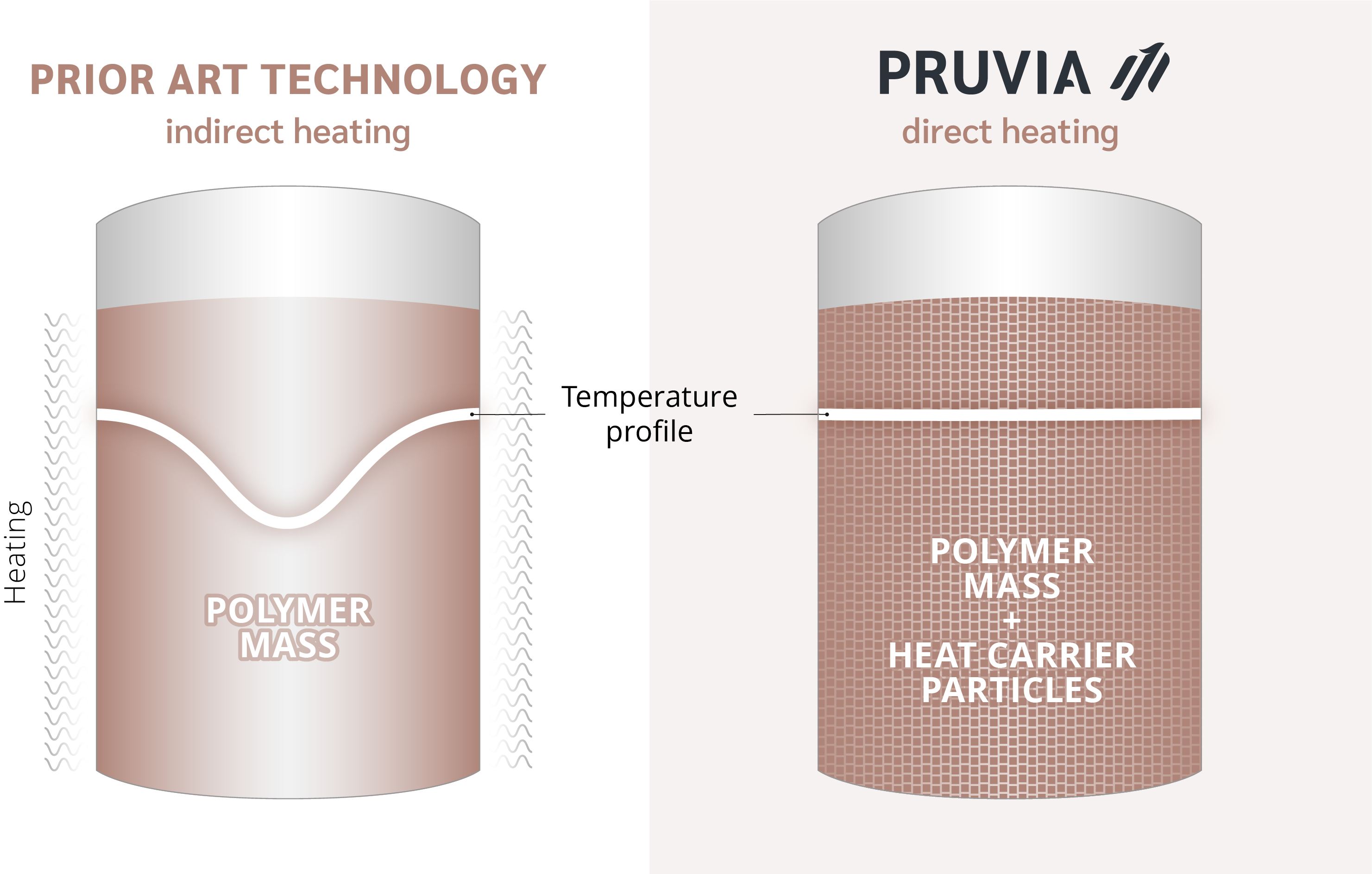
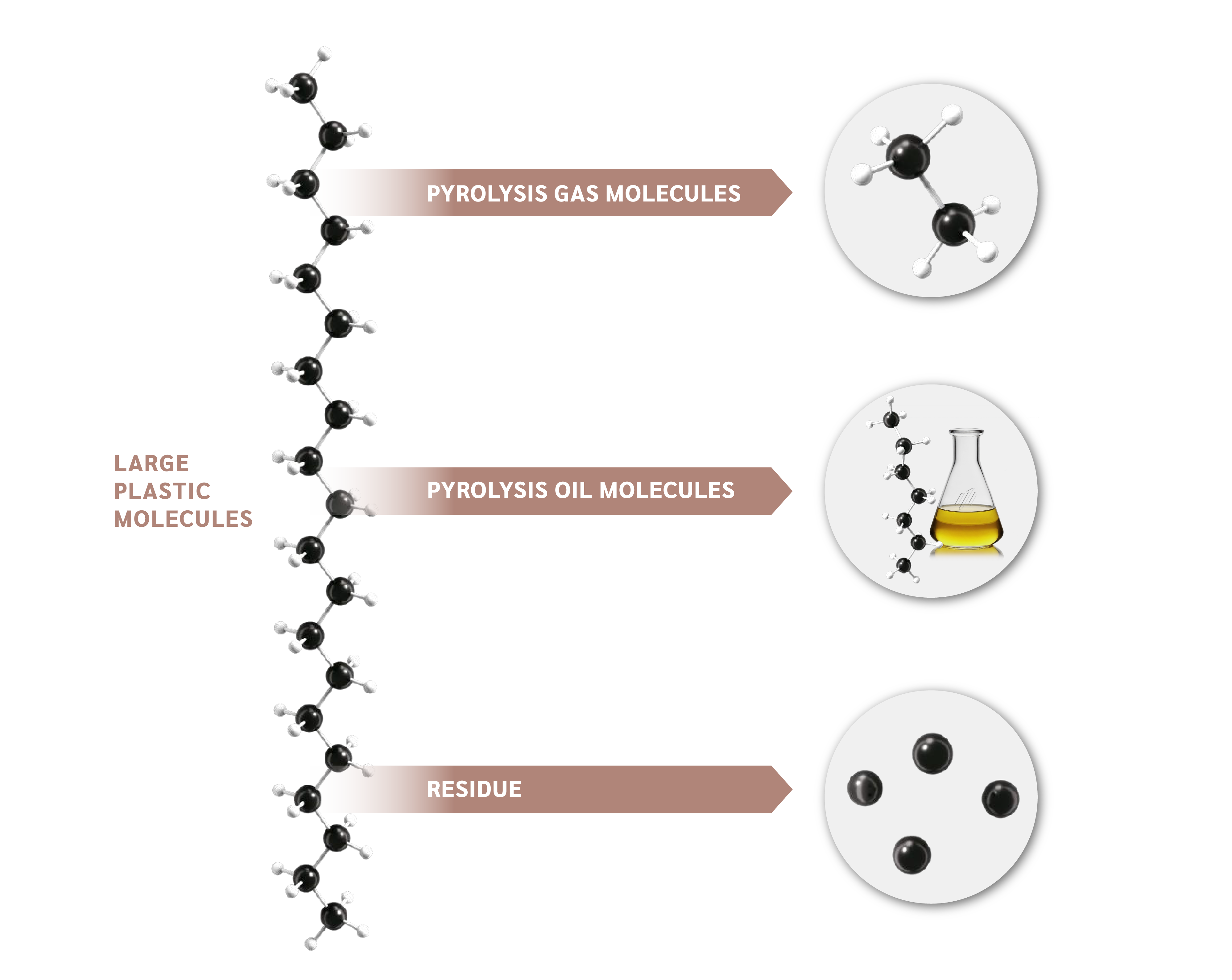
Molecular process
FROM OIL TO PLASTIC
Monomers are the molecular building units for plastic. These monomers are made up of hydrogen and carbon atoms. When combined, they form chained molecular structures such as polyethylene. Our thermochemical process breaks down these chains into molecular fragments of different lengths.
Short fragments of the cracked hydrocarbon chains end up in a gaseous state. These non-condensable gases can be transformed to electricity or further used for heat recovery.
Long molecular fragments are also gases at higher temperatures.
After cooling these condense into liquids such as naphtha. This is the key output of the process and starting point to produce the molecular building units and subsequently new virgin-grade high quality plastic.
The carbon-rich process residue is used internally for energy recovery and is not leaving our process.
BENEFITS AT A GLANCE
CLOSING THE LOOP WITH AN EFFICIENT PROCESS
Our plant is compact and low-maintenance. The homogeneous reaction temperature enables reliable temperature control by heat transfer particles and leads to high-cost efficiency. Learn more about thermochemical recycling, the PRUVIA MLM-R® technology, and the benefits in our comprehensive scientific paper! .
Visit website: Science Direct